The Art of Casting Aluminum: Grasping the Refine
The Art of Casting Aluminum: Grasping the Refine
Blog Article
Opening the Prospective of Light Weight Aluminum Casting: A Comprehensive Introduction
Aluminum casting stands as a foundation in the world of metalworking, providing a plethora of advantages and applications throughout various markets. From its historic importance to the modern-day innovations in casting methods, light weight aluminum has actually constantly verified itself as a useful and functional product. As we navigate with the landscape of light weight aluminum spreading procedures and delve into the ins and outs of quality assurance measures, an extensive introduction of opening real potential of this metal emerges. The possibilities seem endless, promising understandings that might change the means we view and make use of aluminum in production (casting aluminum).
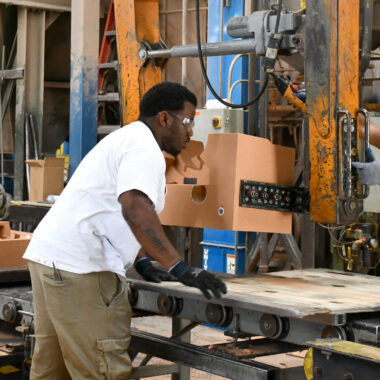
History of Light Weight Aluminum Spreading
Light weight aluminum casting has a rich historic history that goes back to old civilizations, showcasing the withstanding value of this metallurgical process in various industries. When ancient human beings like the Egyptians and the Sumerians made use of rudimentary techniques to cast little objects, the roots of light weight aluminum spreading can be traced to about 5,000 B.C.. It was not up until the 19th century that aluminum spreading saw substantial innovations with the exploration of the Hall-Héroult procedure for removing light weight aluminum from its ore, making it extra accessible for casting purposes.
The adaptability of light weight aluminum casting allowed for intricate forms and detailed styles to be produced with accuracy, even more sustaining its fostering throughout various fields. Today, light weight aluminum casting continues to be a keystone in the manufacturing of a broad variety of products, highlighting its enduring tradition and value in contemporary production procedures.
Benefits and Applications
With its extraordinary strength-to-weight ratio and outstanding thermal conductivity, light weight aluminum casting offers a myriad of benefits and diverse applications throughout numerous sectors. One of the key benefits of aluminum casting is its lightweight nature, making it a suitable option for markets where weight reduction is important, such as auto and aerospace.
In terms of applications, aluminum spreading is widely used in the automotive market for parts like engine blocks, cylinder heads, and wheels due to its stamina and light-weight homes. The adaptability of aluminum spreading prolongs to customer electronic devices, where it is made use of in the production of coverings and warm sinks.
Kinds Of Aluminum Spreading Procedures
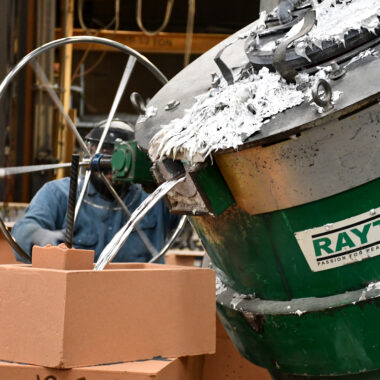
Amongst the various methods employed in industrial settings, aluminum casting processes incorporate a variety of strategies suited to various applications and requirements. One of one of the most common methods is sand casting, where a mold and mildew is produced by condensing sand around a pattern of the preferred part. This procedure is flexible and cost-efficient, making it preferred for both tiny and large-scale manufacturing. An additional widely used strategy is die casting, which includes forcing molten light weight aluminum right into a mold and mildew dental caries under high pressure. Die spreading enables high accuracy and repeatability, making it suitable for producing complex forms with slim wall surfaces. Investment casting, likewise called lost-wax casting, is favored for its capability to generate in-depth and intricate parts with a smooth surface area finish. Lastly, permanent mold spreading includes making use of recyclable steel mold and mildews to create consistent and premium aluminum parts. Each of these light weight aluminum spreading processes provides distinct advantages, satisfying a large range of industrial requirements.
Advancements in Light Weight Aluminum Spreading Strategies
Current innovations in aluminum spreading methods have actually reinvented the manufacturing industry, offering improved efficiency and accuracy in the manufacturing of complicated parts. One significant technology is the development of 3D sand printing technology, which enables the development of elaborate sand mold and mildews with minimal hands-on labor. This strategy permits better More hints style adaptability and faster manufacturing cycles, making it optimal for prototyping and tiny batch manufacturing.
Additionally, making use of sophisticated simulation software program has dramatically boosted the spreading process by making it possible for designers to optimize mold styles and predict potential problems before production starts (casting aluminum). This results in enhanced product quality and lowered product waste
Additionally, the fostering of vacuum-assisted light weight aluminum spreading has actually boosted the total quality of spreadings by lessening porosity and ensuring an extra uniform distribution of liquified steel. This technique is particularly valuable for components that require high structural integrity and premium surface coating.
Top Quality Control in Light Weight Aluminum Casting
The innovations in light weight aluminum casting methods have not just enhanced performance and precision yet have actually also emphasized the important value of quality assurance in making sure the reliability and efficiency of cast components. Quality assurance in aluminum casting involves a methodical technique to check and assess the production process, determining any type of deviations from established requirements that could impact the final item.
One critical element of quality assurance is using innovative innovations such as non-destructive testing methods like X-ray and ultrasound to discover interior issues without jeopardizing the honesty of the actors components. Furthermore, applying rigorous inspection protocols at different stages of manufacturing helps in recognizing and remedying issues promptly, guaranteeing that only parts fulfilling the defined requirements are launched for use.
Additionally, quality assurance expands past the production process to incorporate post-casting procedures like heat treatment and surface area completing, assuring that the final items meet the wanted requirements. By focusing on high quality control actions, producers can enhance item consistency, resilience, and overall consumer satisfaction in the world of light weight aluminum casting.
Conclusion
Different types of casting processes and ingenious methods have actually been learn this here now developed to enhance the efficiency and quality of light weight aluminum spreading. In general, light weight aluminum spreading proceeds to be a useful manufacturing process with excellent potential for further developments in the future.
As we browse via the landscape of aluminum spreading processes and click here to read delve right into the complexities of high quality control actions, a detailed review of unlocking the real possibility of this steel emerges. It was not till the 19th century that aluminum casting saw considerable improvements with the exploration of the Hall-Héroult procedure for drawing out light weight aluminum from its ore, making it a lot more available for casting purposes.
Among the various methods employed in commercial settings, light weight aluminum casting processes encompass a variety of strategies suited to different applications and needs. Investment casting, also known as lost-wax casting, is preferred for its capacity to generate detailed and thorough components with a smooth surface finish. Different kinds of casting procedures and ingenious techniques have been created to improve the performance and top quality of light weight aluminum casting.
Report this page